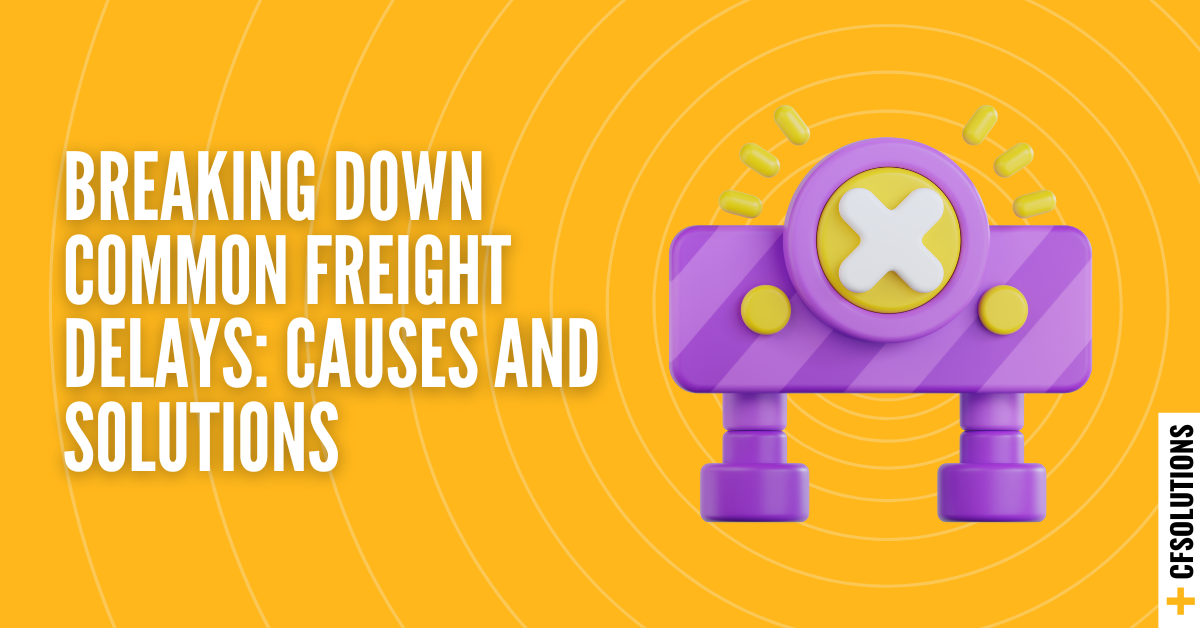
Freight delays can disrupt operations, strain customer relationships, and increase costs. Understanding the common causes behind these delays is the first step in minimising their impact.
Poor Documentation
The Cause: Missing or incorrect documentation, such as consignment notes, manifests, or customs paperwork, can lead to processing delays and compliance issues.
The Solution:
- Ensure all shipping documents are accurate and complete before dispatch.
- Use digital tools to generate and verify documentation automatically.
- Partner with a logistics provider that offers documentation support.
Weather Disruptions
The Cause: Severe weather conditions like heavy rain, floods, or bushfires can impede freight movement, particularly in regional or remote areas.
The Solution:
- Incorporate contingency planning into your freight strategy.
- Partner with carriers experienced in handling weather-related disruptions.
- Opt for multi-modal freight options to reroute shipments if necessary.
Capacity Constraints During Peak Periods
The Cause: High demand during peak seasons like Christmas or EOFY overwhelms carrier networks, leading to bottlenecks and extended transit times.
The Solution:
- Book shipments early during peak seasons to secure capacity.
- Diversify your carrier network to reduce reliance on a single provider.
- Use data insights to forecast demand and prepare accordingly.
Delays Due to Last-Mile Delivery Challenges
The Cause:
Last-mile delivery, the final leg of the shipment journey, often faces inefficiencies in densely populated areas or locations with restricted access, such as gated communities, CBDs, or industrial zones with limited parking and unloading spaces.
The Solution:
- Optimised Delivery Windows: Work with carriers to arrange flexible delivery windows tailored to specific access restrictions.
- Specialised Equipment: Use carriers equipped with smaller vehicles or tailgate loaders for hard-to-reach delivery locations.
- Technology Integration: Implement real-time GPS tracking and communication with drivers to adapt quickly to unexpected access issues or address-specific delivery requirements.
This approach helps streamline the complexities of last-mile logistics, ensuring timely and efficient deliveries even in challenging environments.
Inefficient Loading and Unloading Processes
The Cause: Delays at pickup or delivery points due to long wait times, limited loading bays, or manual handling issues can disrupt schedules.
The Solution:
- Work closely with customers to confirm the availability of loading and unloading equipment and arrange pickup and delivery times in advance whenever possible.
- Partner with carriers equipped with specialised tools, such as tailgate loaders, to streamline loading and unloading processes.
- Utilise tracking systems to monitor operations at loading docks and identify opportunities for increased efficiency.
Customs and Border Delays
The Cause: International shipments often face delays due to customs clearance issues or incomplete import/export documentation.
The Solution:
- Work with freight providers experienced in international shipping and customs processes.
- Ensure all customs declarations and regulatory requirements are completed accurately.
- Use bonded warehouses to reduce delays in customs clearance. Bonded warehouses are secure storage facilities where imported goods can be stored without immediately paying customs duties. This allows businesses to hold shipments while completing necessary customs documentation or awaiting clearance.
Miscommunication Between Stakeholders
The Cause: Lack of clarity or communication breakdowns between customers, carriers, and freight providers can lead to errors and unnecessary delays.
The Solution:
- Use a centralised platform to manage freight operations and improve communication.
- Provide all parties with clear instructions and delivery expectations.
- Partner with providers that prioritise proactive communication.
Lack of Freight Visibility
The Cause: Without real-time tracking, businesses and customers are left guessing about the status of shipments, leading to missed updates or coordination issues.
The Solution:
- Invest in transport management systems (TMS) with live tracking capabilities.
- Share real-time updates with customers to improve transparency.
- Use analytics to monitor and address potential disruptions before they escalate.
Freight delays are inevitable, but their impact can be minimised with the right strategies and tools allowing businesses to maintain reliable operations and strengthen customer trust.
Are you interested in learning more about how customised freight solutions can benefit your business? Or want to reduce freight delays and keep your logistics on track? Contact our team to explore strategies tailored to your business needs.
Subscribe to our Newsletter or Follow Our Socials
Related Posts
- by Customised Freight Solutions
- 0 Comments
What’s Moving Australian Freight Forward in 2025?
It’s hard to believe we’re already halfway through the year. The ...
Read More- by Customised Freight Solutions
- 0 Comments
What’s Behind Your Fuel Levy? A 2025 Guide for Freight Costs
Fuel levies have become a familiar line item on many freight ...
Read More- by Customised Freight Solutions
- 0 Comments
Understanding Air Cargo Freight: A Practical Guide
Air cargo freight plays a critical role in Australia’s logistics ...
Read More